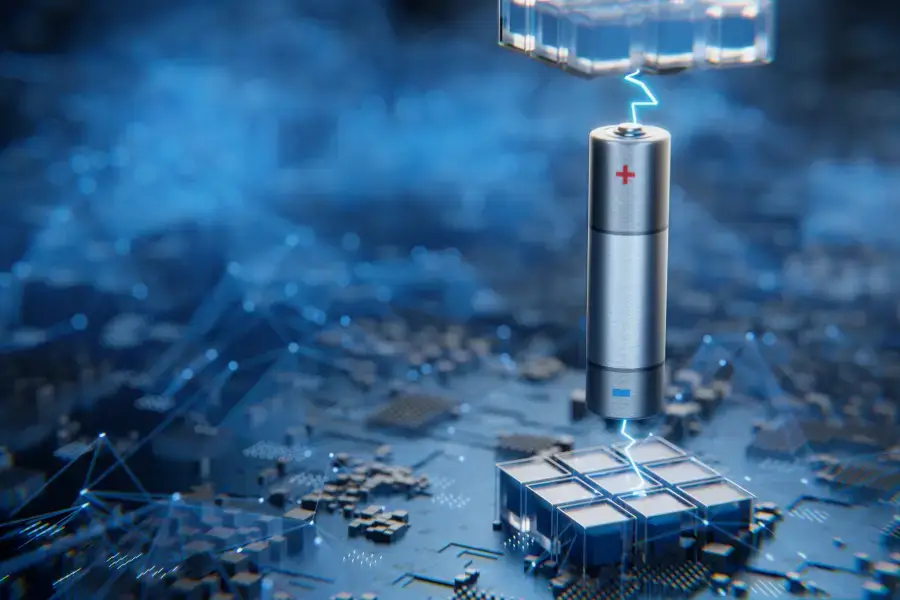
Effective Asset Management for Lead-Acid and NiCd Batteries in Industrial Applications
Introduction
As industries increasingly rely on battery-based energy storage solutions, the management of these batteries becomes critical to ensuring continuous, reliable, and efficient operations. Two commonly used battery types for stationary applications are lead-acid and nickel-cadmium (NiCd) batteries. While both have been essential in energy storage for many years, each type has its own set of unique characteristics, challenges, and maintenance requirements. Proper asset management, from installation to end-of-life disposal, is crucial to maximize battery performance, reduce operational downtime, and extend service life.
In this blog, we explore best practices in the monitoring, maintenance, and sustainable management of lead-acid and NiCd batteries. Focusing on areas such as proactive maintenance, predictive diagnostics, and innovations in battery design, this article aims to provide a comprehensive guide to improving battery reliability, safety, and efficiency in industrial settings.
Monitoring and Maintenance Practices
Lead-Acid Batteries
Proactive monitoring and maintenance are essential for lead-acid battery systems. Implementing a structured preventive maintenance program can significantly reduce the risk of unexpected failures. Regular inspections, including electrolyte level checks and terminal cleaning, are vital components of industrial safety protocols. By adhering to these practices, operators can ensure that batteries remain in peak condition, thus enhancing overall energy efficiency.
NiCd Batteries
For NiCd batteries, asset management strategies should focus on preventing memory effect through diligent maintenance. Regular cycling and appropriate charging techniques are critical to sustaining battery performance. Additionally, proactive diagnostics and inspections help identify early signs of corrosion or degradation, ensuring continuous operation and compliance with industrial safety standards.
Predictive Maintenance and Smart Diagnostics
Lead-Acid Batteries
Integrating predictive maintenance into the asset management strategy for lead-acid batteries can transform operational efficiency. By leveraging data analytics to track performance metrics, operators can identify trends and anticipate potential failures. This proactive approach minimizes downtime and aligns with the goal of achieving zero downtime in operations, thereby enhancing reliability and efficiency.
NiCd Batteries
Predictive maintenance for NiCd batteries requires specialized diagnostics tailored to their unique chemistry. Utilizing advanced monitoring systems enables real-time analysis of performance, helping to detect early signs of capacity loss. Implementing maintenance schedules based on predictive insights not only prolongs battery life but also ensures efficient and safe operations.
Sustainable Materials and Innovative Design
Lead-Acid Batteries
In managing lead-acid batteries, sustainability should be a core consideration. The use of environmentally friendly materials can significantly reduce the carbon footprint associated with production and disposal. Additionally, incorporating innovative designs that enhance thermal management helps minimize energy losses and supports compliance with safety regulations.
NiCd Batteries
For NiCd batteries, effective asset management must address environmental challenges, particularly due to the presence of cadmium. A comprehensive strategy that includes proper recycling and disposal practices is essential. By emphasizing sustainable design principles and material choices, operators can improve energy efficiency while aligning with broader sustainability goals.
Conclusion
Successful asset management for lead-acid and NiCd batteries in stationary applications hinges on adopting smart strategies that cater to the distinct characteristics of each technology. By focusing on optimizing battery configuration, implementing preventive maintenance protocols, utilizing predictive maintenance and smart diagnostics, and promoting sustainable materials, operators can significantly enhance performance and reliability. These strategies not only improve energy efficiency but also contribute to the overarching goal of sustainability, ensuring that energy storage solutions meet future demands while maintaining industrial safety and zero downtime objectives.